Research innovation boosts sustainability in energy industry
On a frigid morning in southern Alberta, a single pumpjack rolls on the horizon before coming to a stop, the rhythmic metal whine dissolves into the quiet of the snowy prairies. This pause in production usually happens once a month at each wellsite and allows time for the water, oil and gas to be separated and measured.
At conventional wells across southern Alberta and Saskatchewan, a wellsite separator is used to determine the production of multiple wellheads. These separators, which can be the size of a car, are unable to measure the production of an individual wellhead in real time, emit greenhouse gases and require personnel on-site to complete the measurement.
Cleaner, faster, more accurate
Now, a newly-developed device, developed by Calgary’s IS Energy with support from SAIT’s Applied Research and Innovation Services (ARIS), brings real-time measurement to the on-shore oil market. Smaller than a carry-on suitcase, this innovation contributes to more sustainable operations, better insights and cleaner energy.
The flow meter — aptly named FLOW, or Flow Optical Wavesensor — can measure the ratio of oil, gas and water as they move together within the same pipe, without needing to separate the three first. This capability allows for real-time monitoring, increased safety, less downtime, reduced calibration needs, lower greenhouse gas emissions and improved efficiency, all while maintaining the tool’s cost-efficiency.
Ariel Torre, co-founder and CEO of IS Energy, approached ARIS’ Centre for Innovation and Research in Advanced Manufacturing and Materials (CIRAMM) to bring their initial design concept of a fully optical multiphase flow meter, which would apply technology developed for NASA’s Mars Rover, to the oilfield.
“Energy security is a critical problem, and our company’s Mars-made innovations in sustainable oil production are catalyzing the transition towards a cleaner energy future,” says Torre.
The result of the applied research project is a device robust enough to withstand the extremes of Canadian weather and the pressure of the output from a wellhead.
“The clear economic benefit for the energy industry, as well as the environmental benefit, has made this project an exceptional fit for CIRAMM and the ARIS hub,” says Evan Altenhof, Research Lead with CIRAMM.
Drilling down to the details
To better understand the problem FLOW is solving, we can think of an analogy to a common measurement instrument in households — the electric meter. In an eight-unit apartment building with one electric meter, all eight units pay one eighth of the electricity bill, but that may not accurately represent their individual use. Installing an electric meter for each unit ensures everyone pays for the electricity used in their specific unit.
Similarly, there are multiple wellheads at each wellsite and their output ratio of oil, water and gas is set each month based on an average measured by the wellsite separator. This output ratio determines production numbers for the owners of the wells and any royalties owed. FLOW is a cost-effective and emissions-free way to measure the output ratio for each individual wellhead in real-time, rather than relying on a monthly average for the whole wellsite pad.
Real-world testing at SAIT’s simulation oil and gas wellsite
After the previous 24 months of development, multiple prototypes and two successful field tests, IS Energy’s pre-commercial product needed a new site for demonstration and further calibration.
Torre, who became a regular on campus while working in CIRAMM’s on-campus labs, found the space they needed after parking his bike in the seasonal motorcycle lot right next to the wellsite right here at SAIT. The Rance Fisher Wellsite Production Education Centre, which is tucked behind the Johnson-Cobbe Energy Centre, is a functional oil and gas production simulation facility.
After some consultation with ARIS and experts from the MacPhail School of Energy, the instrument was installed in the on-campus wellsite in March for further testing, calibration and demonstrations.
“Our flow meter breaks cost barriers, offering full well visibility for precise real-time production optimization,” adds Torre, a 26-year veteran in the energy industry. “Its ultimate value lies in increasing operational efficiency, reducing costs, and reducing environmental impact of oil and gas production."
Industry driven — industry driver
SAIT's Applied Research and Innovation Services (ARIS) team develops new or improved technologies in response to the innovation needs of industry.
Partner with ARISIndustry Driven
We prepare students for successful careers and lives.
SAIT'S
2020-2025
Strategic plan
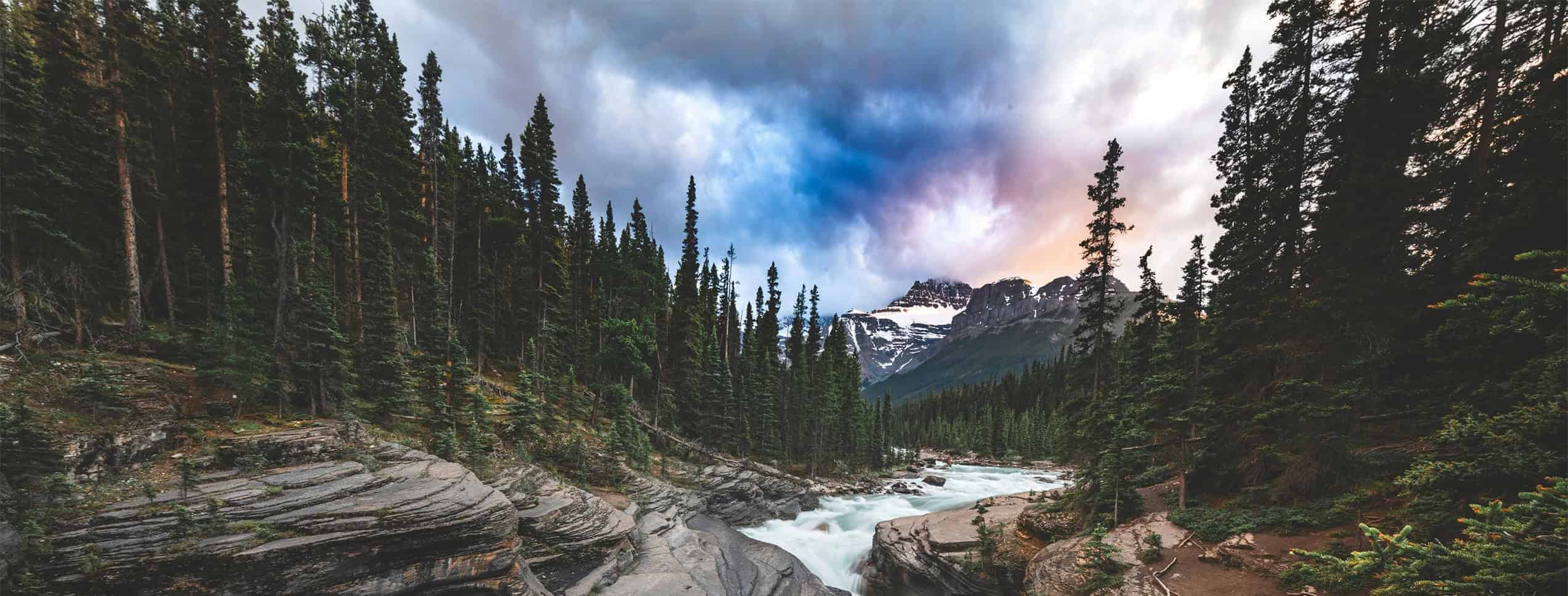
Oki, Âba wathtech, Danit'ada, Tawnshi, Hello.
SAIT is located on the traditional territories of the Niitsitapi (Blackfoot) and the people of Treaty 7 which includes the Siksika, the Piikani, the Kainai, the Tsuut’ina and the Îyârhe Nakoda of Bearspaw, Chiniki and Goodstoney.
We are situated in an area the Blackfoot tribes traditionally called Moh’kinsstis, where the Bow River meets the Elbow River. We now call it the city of Calgary, which is also home to the Métis Nation of Alberta.